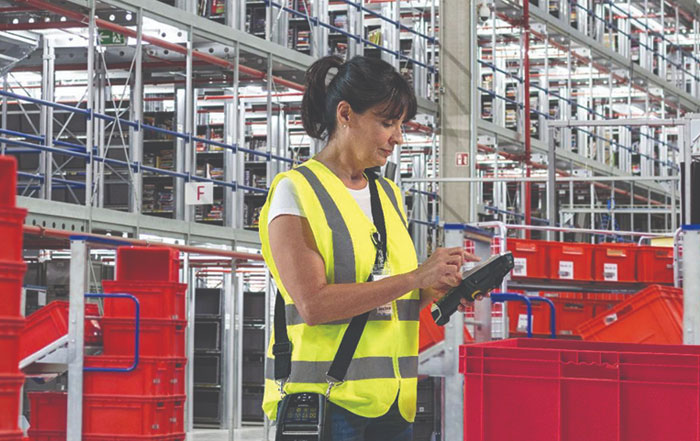
New types of “edge” technologies promise new options for real-time location insights. Learn how these emerging forms of data capture might supplement traditional AIDC as well as the importance of software platforms, analytics and applications that take advantage of real-time location data.
The newest thing in data capture isn’t so much a device people use to “capture” data with, it’s the autonomous gathering of data by sensors and other edge technologies. Even companies that provide mobile handhelds and other data capture devices are onboard with the notion that autonomous capture of real-time location data will be a boon to warehouse operations.
“Data capture devices are only part of the equation,” says Bruce Stubbs, director of supply chain marketing for Honeywell Safety and Productivity Solutions. “Other technologies like sensors and beacons are allowing us to utilize information captured in real time, often autonomously. Today, it’s not only bar coding and RFID (radio frequency identification) data capture that is important, it’s also beacons and sensors and blending these technologies to support a connected supply chain.”
Honeywell, like some other providers of industrial mobile devices, has embraced solutions for real-time data capture and has put more attention on software in recent years. Vendors generally recognize that bar code data collection and some human triggered scanning of passive RFID tags remain vital to supply chains, even while technologies like ultrawideband (UWB) and Bluetooth Low Energy (BLE) beacons can enable new types of real-time locating system (RTLS) solutions. Research firm MarketsandMarkets estimates the worldwide RTLS market will grow from just under $3.2 billion in 2018 to $8.79 billion in 2023, representing 22.5% compound annual growth.
Some warehouses could benefit from technology such as UWB. Unlike traditional bar code scanning with handhelds, today’s edge technologies can pull in data without human intervention. The newer edge technologies also deliver a near real-time stream of data to reveal the position of goods or assets, rather than a point-in-time data grab. That may sound great, but vendors point out that multiple factors need to be considered in sorting through this next-generation technology, including edge hardware and infrastructure costs, how much precision is really needed, the value of the assets/goods to be tracked, and perhaps above all, the software capabilities needed to use the data.
New edge options
Real-time location tracking technology like UWB and BLE beacons aren’t likely to replace more traditional technologies like bar codes. That’s because bar codes are cheap and effective for basic track-and-trace purposes, even if they don’t generate a constant stream of data. Passive RFID tags also have found useful niches, especially in retail supply chains, and today they are relatively inexpensive at the tag-level compared to UWB.
The issue with real-time location tracking technology choices, says Kurt Nehrenz, co-founder and chief of technology strategy with BlueCats, a provider of real-time location solutions, is to select the appropriate technology for each application. As part of that assessment, Nehrenz explains, organizations need to consider the value of the assets or inventory that need to be tracked, the cost of the grid network needed to capture and transmit the data, and payback factors such as whether real-time tracking can significantly increase productivity. “Real-time positioning [technology] is only as good as what it means to the operation,” says Nehrenz.
UWB beacons are highly accurate, but expensive. Nehrenz says roughly $5 per beacon is currently “about the floor” on UWB beacon costs. Given that price level, he adds, UWB beacons tend to get used on assets like picking carts or other moving containers that carry high-value materials. Having pinpoint visibility on such assets can have a payoff by eliminating wasted time looking for materials.
At one company that makes glass panes for the automotive industry, tracking carts in real time with UWB beacons has cut out the time the company previously spent sending people out to locate panes on specific carts. The BlueCats location software is able to do an association between panes of glass with bar codes placed on a UWB-enabled cart, thus providing real-time visibility for every item on every moving cart.
“For some operations, they can lose tons of time trying to find specific high-value items that are on the move,” says Nehrenz. “With our solution, when you associate items to a cart, we give them a software user interface where they can simply type in the ID for any item, and it will immediately show them where it is.”
BlueCats uses a variety of edge technologies, including UWB, BLE, global-positioning system (GPS) sensor data and RFID. Nehrenz says it’s important that a location platform can work with multiple edge technologies. While in some instances a BlueCats software engine is used on its own, through the vendor’s application programming interfaces (APIs), the location engine can pass information to warehouse management system (WMS) or labor management solutions, says Nehrenz.
A good location software engine, says Nehrenz, adds context to raw position data, such as determining when goods or assets move between zones, or if something being tracked crosses into a zone where it’s not supposed to be. “You’re creating and managing rules … so that when things happen, you can do something useful with the information,” he says.
Location-driven systems
Vendors point out that while newer location technology like UWB is exciting, it is the optimization of processes based on location visibility that matters. One vendor with this view is Locanis, a German software provider that offers a supply chain execution software system that leverages real-time positioning beacons and technology, including UWB.
According to Bengt Turner, CEO of Locanis, while at first the company developed its own position tracking hardware, today its focus is on software. Locanis partners with providers of location technology vendors such as Ubisense and Pozyx, using the resulting data to feed the algorithms in the Locanis Site Optimizer system. The system’s functions span WMS, yard management, as well as transportation event management.
“We are completely focused on optimization—on how you distribute tasks to assets and resources in an intelligent and orchestrated way,” says Turner.
Since UWB can pinpoint the real-time position of a resource like a lift truck, a pallet or employees wearing UWB-enabled badges to within centimeter accuracy, the Locanis system uses that insight to assign work in the most efficient way. “Our software algorithms use real-time positioning to select the right resources at the right time … [which] minimizes idle time and empty running of assets,” Turner says.
Within a warehouse, position knowledge over resources and where inventory is placed makes it possible to create efficient storage in a flexible way, thus keeping resources close together to minimize travel and make it easier to interleave tasks, says Turner. Outside the four walls of a DC, real-time shipment tracking and yard operations can be managed by the Site Optimizer software, making use of real-time positioning data fed into the system to optimize dock assignments and yard activity.
Location management in the yard and DC combined with some calculations around demand can also be used by the system to predict when a DC will exceed storage capacity and recommend the movement of empty trailers to a dock area to serve as temporary space, explains Turner. “Real-time position technology opens up a new dimension of things you can’t do normally because you know so much more about where your resources really are,” he says.
Locanis’s users, says Turner, include a global consumer goods company with installations in Germany and China, a global brewer with installations in Austria, and more recently a system is under implementation in Asia by a global manufacturer of heavy vehicles. In addition to working with UWB, laser-based positioning, RFID and bar code technologies, Locanis Production Warehouse System can also use data from sensors on production lines. “The goal is to manage everything as a team of resources that works together in terms of what is happening holistically,” he says.
Software as lever
The key to benefiting from RTLS data is to have software that can monitor parameters and trigger adjustments to operations before problems escalate, says Honeywell’s Stubbs.
“The value comes from a proactive dashboard,” says Stubbs. “If you’re just looking at trends after the fact, it might as well be a written report.”
For example, says Stubbs, Honeywell’s Operational Acuity solution is able to take the latest activity data from Honeywell voice-enabled warehouse solutions and spot trends such as a pick location being skipped or delays at certain locations, so managers can take action. Similarly, Honeywell’s warehouse execution system (WES) solution, known as Momentum, is able to monitor the real-time progress of work going through a warehouse’s automated materials handling systems and see if work is starting to slow down or if certain actions should be taken to smooth out the flow of order fulfillment work.
Stubbs sees real-time location data from beacons or sensors as another source of data capture that can feed into proactive analytics in solutions such as Operational Acuity or Honeywell’s WES. Ideally, he adds, managers should be able to “subscribe” to specific types of real-time data of interest. The range of technologies involved might span bar codes, RFID, location beacons, real-time view of automation with WES, or voice system activity and trends.
“It’s a bigger picture now,” says Stubbs. “Data capture spans all these disparate pieces of technology that capture data, and instead of throwing it into a big bucket it’s now a matter of logically parsing it into buckets of information that people can subscribe to.”
Another key to effective leveraging of technology like UWB beacons is the flexibility and capability of the “location engine” or software platform that takes in real-time data, establishes location insights, and filters data to trigger alerts and actions, says Mark Wheeler, director of supply chain solutions for Zebra Technologies. In addition to bar code scanning devices and solutions, Zebra has expanded over the years into RFID, RTLS, and has an Internet of Things (IoT) information platform called Savannah. The Savannah platform’s location engine that handles data from UWB and other edge technologies, says Wheeler, is an outgrowth of Zebra’s RTLS solutions business.
According to Wheeler, location engine software should be able to work with multiple edge technologies. “The key is that as we integrate more RTLS technology into more and more business processes that we make the capturing of the data, the securing of the connections to the edge devices, the analytics and the access to that information as standard and as straightforward as possible,” he says.
Core functions of a location engine, Wheeler explains, are mapping and positioning knowledge for each asset being tracked. Using that real-time view, an engine can generate alerts—such as an asset leaving one area or zone of a facility and entering another—that might be useful to a system used for warehouse execution or labor resource management. Such alerts can be run and handled within Savannah, Wheeler says, but the platform is also capable of sending out alerts to a WMS or other execution system.
Wheeler agrees with the view that multiple factors like value of the asset and cost of the hardware play into which edge technology best fits an application. UWB is well suited to high-precision tracking of assets or people (using special tags embedded in employee badges), while for many types of inventory, RFID or bar codes may provide adequate visibility.
Within warehousing and manufacturing locations, Wheeler adds, one of the top applications for RTLS is to track the location of returnable transport items (RTIs). Location technology can prevent RTIs from getting lost, says Wheeler, in addition to knowing where the goods on RTIs are at any given time.
“The goals with real-time location tracking generally are to drive high levels of asset utilization … and minimizing or eliminating the loss of RTIs through better visibility over those assets,” Wheeler says. “The visibility you get with RTLS also helps to error-proof operations. For instance, a solution can use RFID to monitor the movement of goods on a dock and generate a notification if something has been sitting on a dock too long. It’s about leveraging tags and sensors to automatically generate actions to prevent problems, rather than just detecting a problem after the fact.”